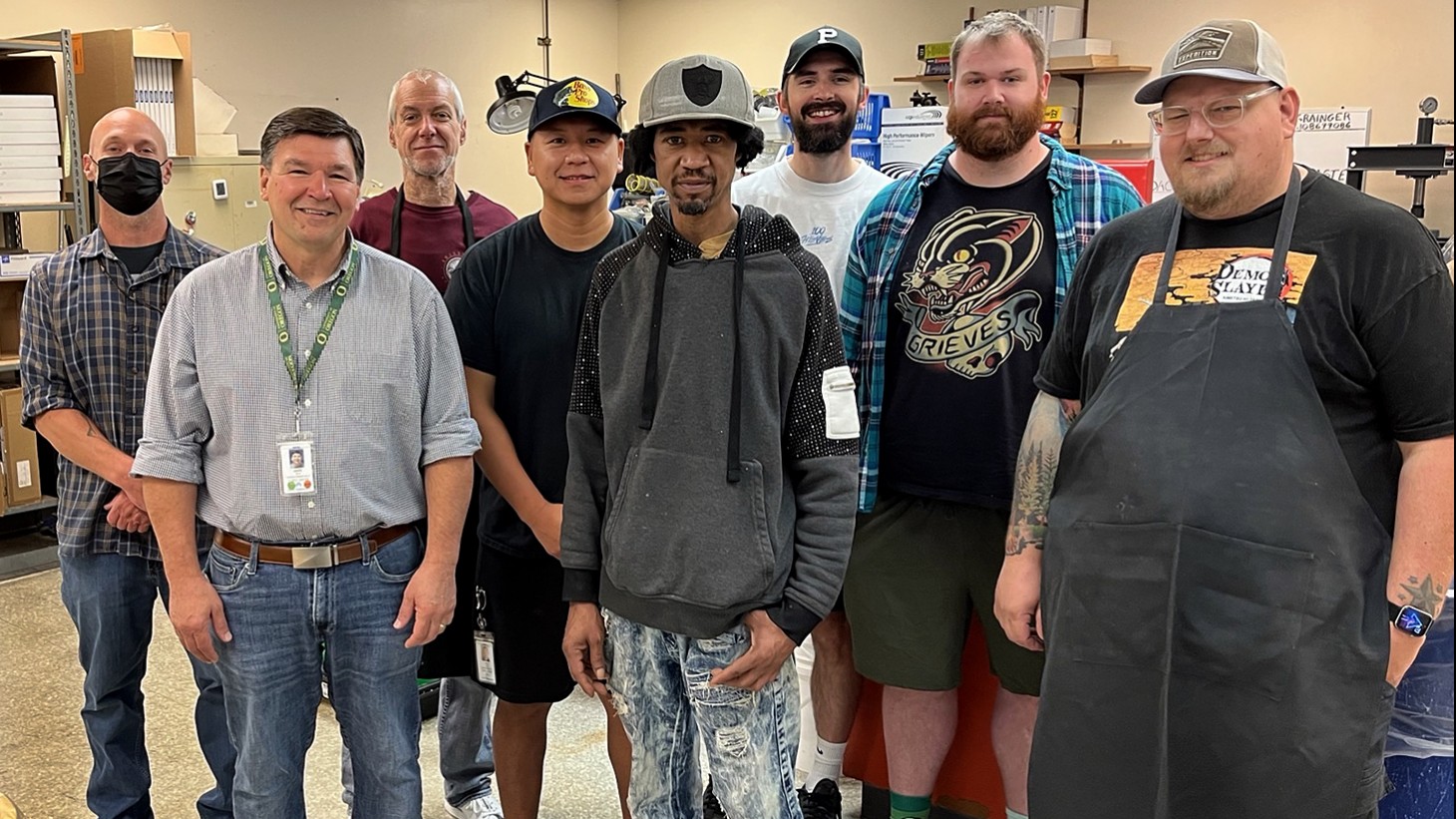
Technicians in the Optical Lab Surface department in the Northwest solved a problem damaging eyeglass lenses for KP members.
Techs overcome problem damaging new eyeglass lenses
If one word inspires dread in the Optical Lab Surface department, it is “swirl.”
The Northwest team helps make eyeglasses for Kaiser Permanente members. Their work is sometimes complicated by swirls – circular scratches on the lenses that can occur during the production process.
In 2022, the team - based at Kaiser Permanente Sunnyside Medical Center outside Portland - grappled with a mysterious increase of swirls.
“Normally, we will get about one swirl per day that we can’t polish out,” says Rodney Edwards, department supervisor and the team’s management co-lead. “But suddenly we were seeing 12 or 13 per day. We knew we were dealing with something very strange.”
When extra polishing can't remove a swirl, the team must fashion a new set of lenses. This raises costs and slows production, delaying delivery of eyeglasses to KP members.
By conducting a painstaking review of its processes, the team uncovered the cause of the swirl surge and improved care and service.
When everyone participates in performance improvement, the better the results and the stronger the work environment. Collaborating on performance improvement also advances a culture at KP in which continuous learning and improvement come naturally.
From technicians to sleuths
Finding the source of the swirls was not easy. The Level 4 team prepares about 700 eyeglass lenses each day.
“It’s tough for us to troubleshoot these things," says Dustin Rushing, an optical lab technician and OFNHP Local 5017 member, who is the team's labor co-lead. "We’re operating at such a high volume we can’t really stop the presses."
To identify the problem, the team performed multiple tests of change.
Team members analyzed vats of liquid lens polish. They improvised new polish filtration devices. They scrutinized surfacing procedures and the calibrations of each piece of machinery. The tests and tweaks occurred while the team tried to keep up with high demand for eyeglasses.
Weeks of testing uncovered the problem: wear and tear on machinery was leaving metal shavings in liquid used to polish new lenses. The solution? Modifying worker procedures and intensifying maintenance and replacement of machine parts.
As a result, the team saw a 94% reduction in swirls during the first 4 months of 2023. That success continues. The team reduced monthly costs to replace damaged lenses, from $525 to $31, for a projected annual savings of $6,000.
While the cost savings may seem small, it illustrates the impact of unit-based teams. Enterprisewide, more than 3,600 teams contribute to KP’s national leadership in measures of affordability, quality, service, and care.
The project earned the optical lab team a UBT Excellence Award from regional leaders.
“The biggest reason for this project’s success was the openness and communication between us all,” Edwards says. “That really opened up some doors for us as a team.”